Schmidt |Sweeper|Swingo 200⁺
Sweeping technology
The Swingo 200+ is available with two independent sweeping systems. A pushed 2-brush system with a brush diameter of 850mm or a pulled 3-brush system with a brush diameter of 800mm. Both systems can be operated either independently or as a dependent system with convenient controls on the driver's door. The brush speed and the pressure can be infinitely adjusted. The brush can be chosen between plastic, steel or mixed trimmings, while the suction nozzle can be selected between rollers or runners.
The 2-brush system with independently controllable circular brushes guarantees absolute mobility in every sweeping situation. Two stable brush arms with integrated buffers allow sweeping widths of up to 2,900mm. Independent brush control is available as an option: separately controllable brushes, up/down, left/right, contact pressure control. This also guarantees clean sweeping results with minimum wear and tear. The brush always returns to its basic position, even when the road conditions change. A version for heavy weed use is also available with additional hydraulic tilting functions for the brush.
The 3-brush system with freely movable front brush arm offers a wide range of options and a sweeping width of up to 2,600mm. Left-right alignment of the front brush is just as possible as sweeping on two levels or heavy weed brush use. All functions of the front brush are hydraulically controlled, including the brush support pressure. The brush unit under the cabin ensures optimum feed of the sweeping material to the suction shaft, while an overlap is always guaranteed. As an option, the side brushes can also be extended hydraulically and their angle can be adjusted, making it asdapatble to any ground conditions during sweeping operations.
Suction and water system
For the 2-brush system, there is a choice of a basic suction shaft with hydraulically operated coarse dirt flap or an HS suction shaft, which combines the advantages of an integrated coarse dirt flap with optimum air flow. The HS suction shaft guarantees maximum suction power even at low speeds. This can save up to 15% in operating costs.
There is an airflow-optimised suction shaft for the 3-brush system, which does not require a separate coarse dirt flap. Coarse debris can only be easily collected by tilting the suction shaft.
The Swingo 200+ is certified with the best level PM10 4-star and PM2.5. The certificate is considered a quality feature throughout Europe and awards four stars in the PM10 test for the highest level of air pollution control as well as the best possible absorption performance with PM2.5.
With the unique Koanda air circulation system and the combination with the pressurised circulating water system, the emission of harmful fine dust is reduced by up to 70%. A large part of the dust-laden air sucked in remains in the suction system and is returned to the suction mouth in a circuit. The small amount of residual air remaining is cleaned by a fine-pored filter. In addition, the Koanda circulating air system impresses with reduced noise emission, low water consumption and allows sweeping at slightly below-zero temperatures.
The proven pressure circulation water system returns large quantities of circulating water to the circuit by means of a waste water pump for reuse. The water recovery system, with a screen surface of 3.3 m2 in the container, not only saves fresh water, but also makes optimum use of the container capacity. By filling water into the hopper (up to 250 litres), the operating range can be increased by up to 50%. The collected swept material is both moistened and compacted. The electric fresh water pump supplies the spray nozzles on the circular brushes. The water quantity for the brushes can be conveniently controlled from the cab.
Sweeping material hopper
The hopper with a system volume of 2m³ enables maximum sweeping capacity and a large radius of action. The hopper is made of corrosion and seawater resistant aluminium. A large dumping height of 1400mm enables emptying into all common dirt containers. The suction pipe in the hopper is optionally available in wear-resistant stainless steel.
Ergonomics and comfort
The spacious cabin is equipped with high quality noise and vibration insulation (72 dB(A)). The front windscreen, which extends down to the floor, and the viewing window in the cab floor provide an optimum view of the sweeping unit and suction nozzle. The excellent all-round visibility contributes to a pleasant working environment and thus supports safe operation in road traffic.
The standard and powerful air conditioning system creates a pleasant and cool working climate even at high outside temperatures. Fresh air is sucked in and filtered at the rear of the cab, while the cab air filter is designed as a pollen filter.
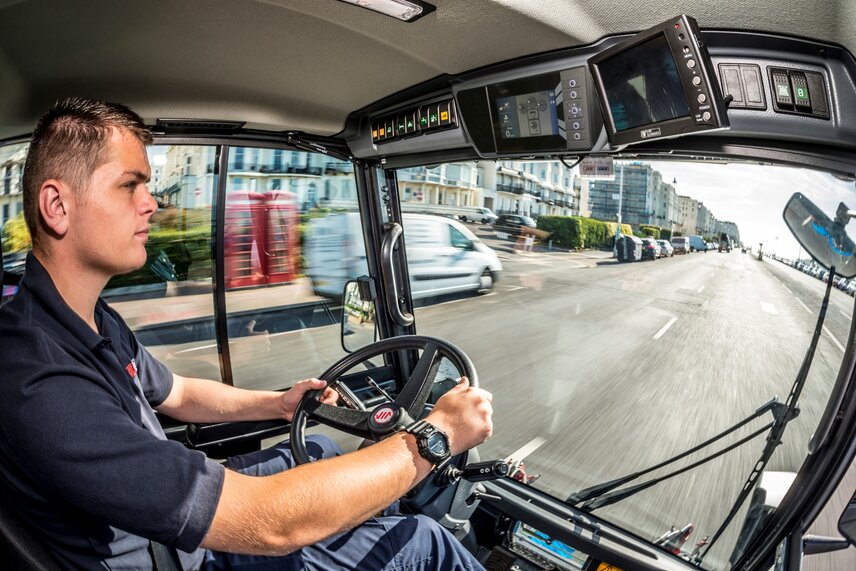
The sweeping unit is controlled via the door control panel with joysticks and push buttons. With the Auto-Drive option, all sweeping functions and the driving commands in sweeping mode can be conveniently operated via the ergonomically- shaped multifunctional control lever. Driving and sweeping from a single source also means greater safety and less stress. The most important information is visible at a glance on the colour display in the roof console. With the help of the onboard diagnosis system, any faults can be localised quickly and efficiently, while a mechanic can make machine-specific settings on the display.
Smooth steering with a height and angle adjustable steering column, cruise control, minimal pedal forces, a comfortable driver's seat with AGR certificate ("Campaign for Healthy Backs") as well as operating and control instruments in an optimum grip area round off the performance features of a modern, ergonomic workplace.
Drive
The basic version has a powerful EuroMot 5 engine with 55kW (75hp), which provides high torque and works without additional urea (AdBlue). As an alternative, a Euro 6c engine with 62kW (84hp) is available, with a modern exhaust after-treatment system with diesel oxidation catalytic converter, closed particle filter system, plus urea injection (AdBlue) and SCR catalytic converter. Unique in this machine category is the compact integration of the four-cylinder Euro 6c engine with the same wheelbase as previous versions. The engine and AdBlue tank are perfectly integrated into the chassis so that the manoeuvrability of the Swingo 200+ is not compromised.
Combined with the powerful hydrostatic transmission, this makes driving and working comfortable and economical. The hydrostat with drive on the rear axle is continuously variable with automatic load-dependent control, providing car-like driving and speeds of up to 50km/h. An electric parking brake system with hill start assistance has been integrated into the travel drive since the last development. In the optional Eco mode, the maximum transport speed can be achieved with reduced diesel engine speed, which leads directly to reduced operating costs and emissions.
Modern vehicle technology
The hot-dip galvanisation of the entire vehicle frame, the suction mouth and important steel components, including the dirt container, provide high-quality corrosion protection.
The hydropneumatically suspended chassis with hydrostatic drive and large 15" wheels offers the highest level of driving comfort in this machine class. The high load capacity and large contact areas of the wheels ensure increased safety with low ground pressure, regardless of road and weather conditions. Optionally, the permissible gross weight can be increased to 5 000 kg. The suspension package, which includes a mechanical optioon, is perfectly matched to the machine, and ensures safe and comfortable driving just like a car. Good driving comfort, robustness and freedom from maintenance are all optimally combined.
A lowerable running gear (optional) simplifies driving in multi-storey car parks and low entrances. The chassis can be lowered by around 70mm at the push of a button and the system levels itself automatically.
The switchable all-wheel steering makes extremely tight turning manoeuvres possible. The all-wheel steering is monitored by means of steering angle sensors, which enables automatic centring, and is both user-friendly and safe.
A hydraulic dual-circuit brake system with disc brakes on the front and rear axle is fitted as standard.
Wide range of options
- Koanda air circulation system
- Rear view camera and suction shaft camera
- Weed brush including additional hydraulic tilting functions
- Hand suction hose
- Pressure washer
- Sound insulation package
- Scrub deck
- Sink drawer cleaner
- Automatic central lubrication system
- Auto-Drive (control lever operation)
- Lowerable landing gear
- High quality LED products
- Winter maintenance attachments
IntelliOPS telematics platform
If you want to monitor, plan, control in real time, optimise or, for example, bill third parties for the activities of your Swingo 200+, then use the digital solutions on our IntelliOPS platform. IntelliOPS supports you in the efficient use of your individual machine as well as in a network with several machines, including those of other brands. Here you can find out more about our digital solutions and how you can use them in a way that is modular and adapted to your needs.