Schmidt |Spreader|Stratos 4.0 - 12.0 m³
Mounting and demounting systems
Maximum safety – Mounting and demount systems
The key components and sturdy construction of the Stratos spreaders are designed for maximum safety and stability, especially during mounting and demounting.
The Stratos spreaders are available in two basic variants:
- For demount legs, hooklifts and fix-mounted systems
- For the ro-ro (roll on/roll off) system.
Both variants can be demounted with a full hopper and full brine tanks.
The new ro-ro system – Even better and easier to use
The further development of the ro-ro system enabled us to make efficient improvements in trailer operation, as the 40cm increase in clearance permits the use of a trailer or a mobile warning sign. In addition, the small tipping angle and the safety belt provide maximum safety while mounting and demounting.
Dosage and conveyor systems
Conveyor belt system
The Stratos systems combine efficiency with safety; the conveyor belt system provides a reliable means of practical every day applications. The integrated conveyor belt is fibre-reinforced, and its V-profile ensures even transportation of the spreading material, while a stainless steel guide plate makes it possible for the belt to glide at full surface contact and minimum friction.
The precise dosage of all commercially available spreading materials is enabled by the accurately adjustable belt speed as well as a feed gate. The feed gate is equipped with an integrated lump-crushing function to ensure a flawless spreading operation; lumps are broken up at constant pressure, preventing stones and foreign particles from blocking or damaging the system. The constant feed rate allows for high dosing accuracy, irrespective of the spreading material’s moisture content, while fitted chains ensure the controlled delivery of the spreading material to the chute. The optimised belt cleaning system prevents salt from running onto the truck’s loading platform, improving the vehicle's ease of maintenance. The lateral sealing between the hopper and the conveyor belt by vertical belt wipers adds to the simplified maintenance required.
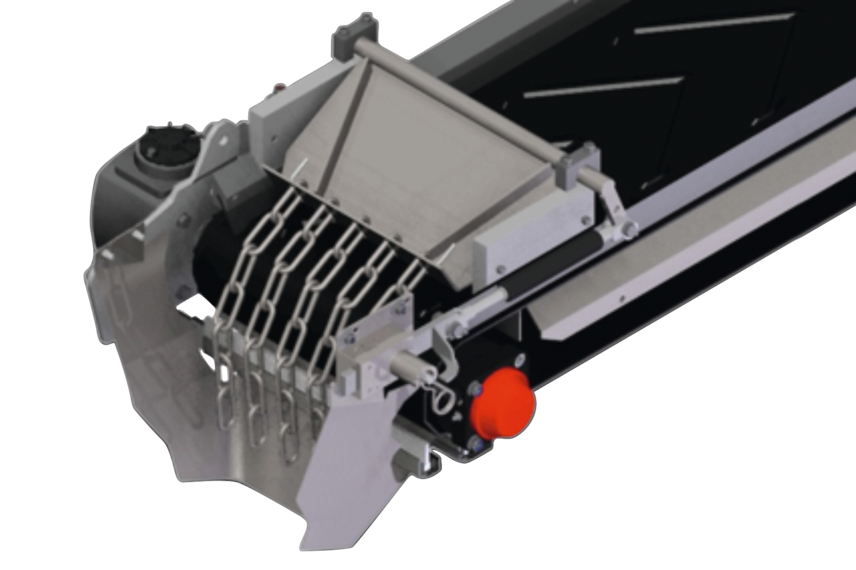
Auger system
The basic component of the Stratos auger system is a Flex auger with two-stage pitch. It is a cold-formed spiral with an open structure that allows for effort-saving transport at low breakaway torque. A variable thread ensures even discharge of the hopper, having a direct positive effect on the centre of gravity of the truck’s spreader. Our new dosing disc achieves even dosage, which is guaranteed by a closed-loop control circuit. Meanwhile, continuous target-to-actual comparisons ensure accurate and constant speed of the system. A cover fitted as standard relieves the auger of the spreading material’s load, noticeably increasing its service life. The auger system is driven by a high-torque hydraulic motor and ensures safe and reliable start-up.
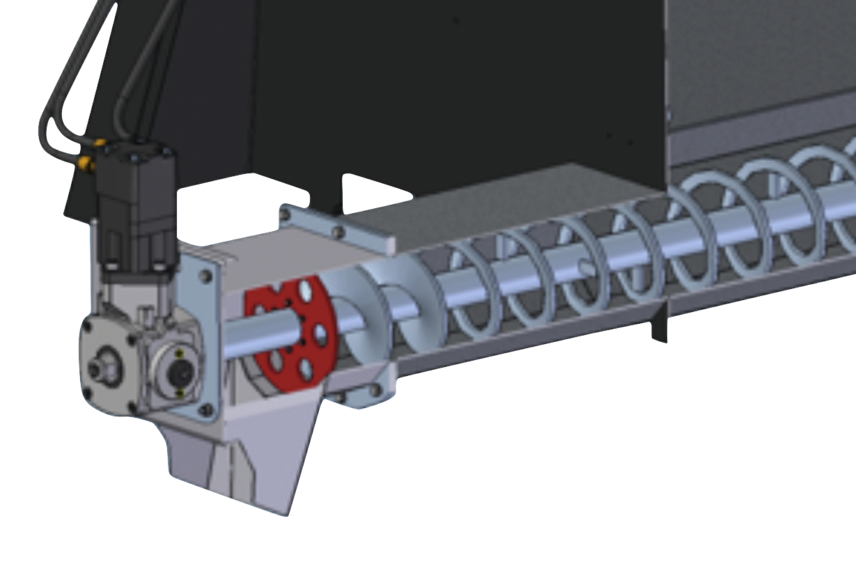
Pre-wet equipment
The Stratos pre-wet equipment is accurately adapted to the hopper size, the capacity of which has been increased, permitting an individually adjustable pre-wet salt admixture of FS 25 to FS 35. The laterally situated liquid tanks with integrated baffles are made of impact-proof and cold-resistant polyethylene. The point of intake is located at the centre of the tank, which permits trouble-free operation even in challenging hilly or mountainous regions. The integrated level indicator enables drivers to always keep track of the spreading material consumption, while the stainless steel filling and drain connection ensures reliable filling, which is considerably accelerated due to the integrated valve-filter combination, large duct cross-sections and maximum user friendliness. When switching on the brine (FS 30), the dry material is automatically reduced and the distribution system settings are optimised in accordance with the change in composition of the de-icing agent. The system achieves a high level of accuracy, thanks to integrated sensors for comparison of the actual versus the target value of the control loops.
Distribution systems
Premium distribution system
In order to apply the spreading material as efficiently as possible, we have advanced our distribution systems to achieve the best possible material flow by integrating a PE chute and optimising the outlet angle of our mixing system. This is enabled due to the path of the spreading material, which is transported via the Premium mixing system to the centre of the spreading disc and is optimally distributed until it is discharged. As a result, a homogenous mixture is produced, which is ejected dynamically as a concentrated jet against the direction of travel.
Premiumplus distribution system
The Stratos Premiumplus mixing system is a further development of our Premium mixing system. In the plus variant, the mixture of salt and brine is completely prepared in a mixing chamber by means of centrifugal force and rotary movement. The rotary mixing chamber is operated electronically via the control panel and can be set to create either a symmetrical or an asymmetrical spreading pattern. The optimised scoop geometry and dimensions ensure a high level of precision over the selected spreading widths of 6.6 - 32.8 ft, 9.8 - 39.4 ft or 13.1 - 45.9 ft.
Kick-back protection on the spreading disc
On contact, the entire distribution system folds away to the back, preventing damage to the spreader.
Drive options
The Stratos drive systems are designed for maximum efficiency at minimum costs.
Vehicle hydraulic system – The municipal solution
In this variant, the spreader is simply powered by the existing hydraulic system of the carrier vehicle. The regulation of the power requirement in LS hydraulic systems means that, due to the low power required during spreading operations, the carrier vehicle needs to share less performance, with lower fuel and oil consumption.
Wheel drive – The conventional solution
The drive power comes from a separate wheel running at the rear of the truck. The wheel’s position has been optimised to enable easy and trouble-free connection to the driveshaft for discharge.
Innovative, CO2-neutral Rotopower – The patented solution
In this system, the required drive power is taken directly off the rear wheel hub and used to further power the vehicle, thus creating a fuel-saving solution with optimum performance.
Engine drive – The vehicle-independent solution
The diesel engine is integrated at the front of the spreader, which reduces the required body length. The start/stop function can now be actuated both via the control panel in the cab and directly on the engine. The performance of the engine drive has also been designed to have minimum power requirements, resulting in low fuel consumption.
Control and information systems
The Schmidt EvolutionLine comprises three operating concepts and provides professional solutions to make de-icing easier and more efficient. Their modular structure offers a completely flexible configuration, making it possible to precisely adapt the control panels to the required needs.
ES control panel – The premium solution
The ES control panel of the Schmidt EvolutionLine is the smartphone among the control panels that meets all current and future operational requirements. The frost-proof 7” colour touchscreen display is sited in a splash-proof, sturdy housing and ensures comfortable handling, plus a long service life. The spreading density, spreading pattern and spreading width are adjusted via ergonomic click-turn control knobs, while eight illuminated push buttons operate the primary and menu-dependent functions. Equipped with optional additional components, the ES control panel can be easily upgraded to become the high-tech control centre of the spreader.
Overview of add-on modules:
- Voice confirmation for commands
- Rear camera view directly on the display
- IntelliOPS: GPRS modem for online data transfer
- GPS for position location
- Route Assistant: GPS-guided spreading operations with route guidance
- ThermoLogic: Temperature-dependent dosage
EP control panel – The extendable solution
The EP control panel is an extendable solution that can be flexibly adapted to meet the required needs. The control panel has an ergonomic design in a sturdy housing, while standard equipment comprises a frostproof, backlit display, ergonomic click-turn control knobs, plus illuminated push buttons that can be assigned individual tasks.
Overview of add-on modules:
- IntelliOPS: GPRS modem for online data transfer
- GPS for position location
EC control panel – The entry-level solution
The compact EC control panel meets all basic requirements and permits easy and smooth operation of the spreader. Thanks to easy to use buttons, handling is very straightforward and complemented by ergonomic click-turn control knobs fitted as a standard.
IntelliOPS telematics platform
If you want to monitor, plan, control in real time, optimise or, for example, bill third parties for the activities of your Stratos, then use the digital solutions on our IntelliOPS platform. IntelliOPS supports you in the efficient use of your individual machine as well as in a network with several machines, including those of other brands. Here you can find out more about our digital solutions and how you can use them in a way that is modular and adapted to your needs.